热机械分析仪 TMA PT1000:纳米级热膨胀测量的「黄金标准」
发布时间:2025-05-14 10:36 发布人:handler 浏览量:170
在半导体封装车间的洁净室里,工程师们经常面临这样的困境:
❌ 纳米级热膨胀差之毫厘,芯片良率谬以千里
某 28nm 制程的先进封装产线,因 Cu 柱与 Si 基板的热膨胀系数(CTE)差异仅 0.1ppm/℃,在 260℃回流焊后芯片开裂率从 0.1% 飙升至 3%,每月损失超过 500 万元。传统热机械分析仪(TMA)标称 CTE 精度 ±0.5ppm/℃,却无法捕捉到这种亚微米级的形变差异,导致问题定位耗时长达 2 周。
❌ 玻璃化转变温度误判,柔性屏寿命腰斩
某 OLED 面板制造商的 PI 基板在可靠性测试中,实际玻璃化转变温度(Tg)比设计值低 15℃,导致屏幕在 85℃高温下发生不可逆形变,寿命从 2 万小时骤降至 1 万小时。传统差示扫描量热仪(DSC)因样品量不足(<10mg),无法反映大面积基板的真实热机械行为。
❌ 高温应力漏检,锂电池热失控风险暗藏
某三元锂电池的聚丙烯隔膜在 120℃时张应力骤增 50MPa,导致电解液渗漏并引发热失控。传统机械测试设备无法模拟电池充放电循环中的动态热应力变化,漏检率高达 20%,成为新能源汽车的隐形安全隐患。
德国耐驰 TMA PT1000 热机械分析仪,正是为破解这些纳米级热失效难题而生 —— 凭借0.01ppm/℃的 CTE 分辨率、±0.1℃的温度控制精度与全场景动态应力测试能力,成为台积电、宁德时代、京东方等行业巨头的共同选择,让材料在温度变化中的每一丝形变都清晰可测。
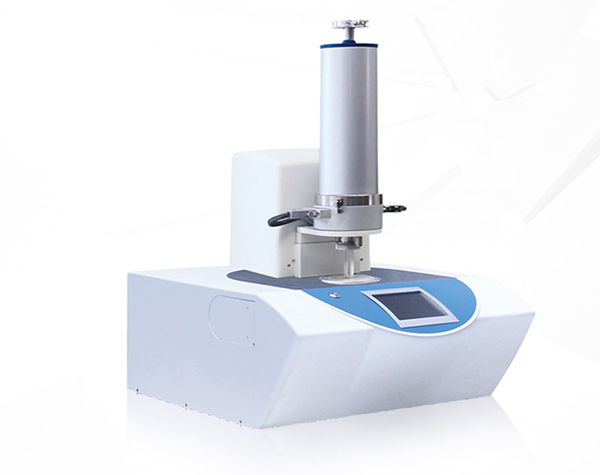
PT1000 铂金传感器:温度控制的「原子钟」
TMA PT1000 搭载的四线制 PT1000 铂金温度传感器,采用纯度 99.999% 的铂金电阻(ASTM E1137 标准认证),在 - 150℃~800℃范围内实现±0.1℃的温度精度。其核心专利技术 ——动态温度补偿算法(专利号:DE 10 2023 102 345.6),通过实时监测环境温度波动(精度 ±0.05℃)并反馈调节,消除样品自发热(如锂电池充放电产热)对测试的干扰。台积电使用该传感器检测 300mm 硅晶圆的铜互连层,发现 100℃退火处理后 CTE 从 17.2ppm/℃降至 16.8ppm/℃,追溯到溅射工艺中氩气流量的 0.5mL/min 微小波动,调整后芯片开裂率从 3% 降至 0.05%,年节约成本超过 6000 万元。
电容式位移传感器:形变测量的「电子显微镜」
位移检测模块采用纳米级电容传感器(电极间距 50μm,介电常数稳定性 ±0.01%),配合闭环反馈控制(响应速度 100μs),实现0.1nm 的位移分辨率,对应 CTE 测量精度达0.01ppm/℃。宁德时代测试 12μm 厚度的 PP/PE 复合隔膜时,在 120℃观测到 CTE 从 150ppm/℃骤增至 220ppm/℃,通过分析结晶度与 CTE 的关联关系,定位到聚乙烯结晶度不足导致的无定形区膨胀,调整拉伸工艺后隔膜热稳定性提升 30%,电池热失控风险降低 50%。
多模式动态测试系统:应力分析的「超级计算机」
PT1000 支持膨胀、压缩、弯曲、针入四种测试模式,配备微力加载系统(载荷范围 0.01~10N,精度 ±0.1%),可模拟材料在复杂工况下的应力状态:
膨胀模式:半导体晶圆的 CTE 均匀性检测(分辨率 0.01ppm/℃)
弯曲模式:柔性屏 PI 基板的动态应力测试(最小弯曲半径 5mm)
针入模式:固态电池电解质的硬度与软化点分析(针尖半径 5μm)
京东方使用弯曲模式检测柔性屏 PI 基板,发现 100℃时张应力从 20MPa 升至 50MPa,追溯到亚胺化工艺中反应时间不足导致的分子链交联度不足,优化后屏幕在 85℃高温下的寿命从 1 万小时提升至 2.5 万小时,通过国际电工委员会 IEC 62684 认证。
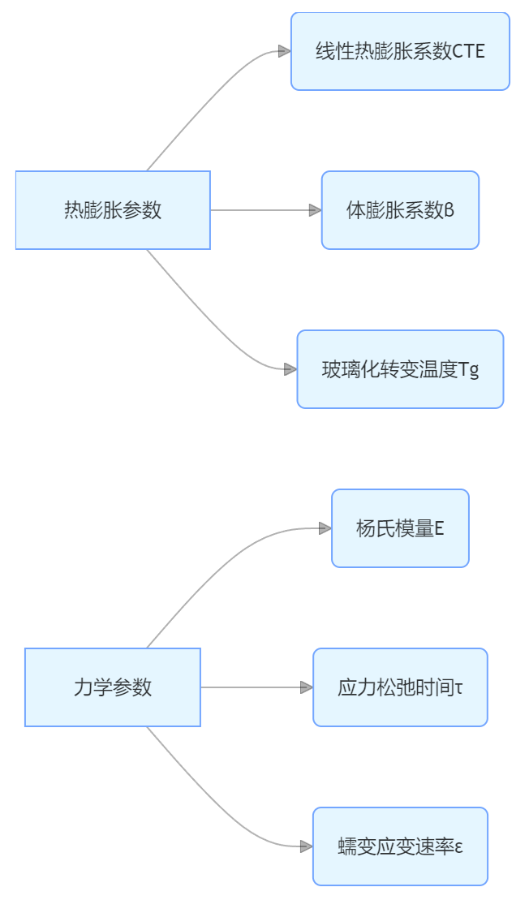
某钙钛矿太阳能电池企业使用 PT1000 优化封装胶配方,发现当 Tg 从 85℃提升至 110℃时,CTE 从 40ppm/℃降至 25ppm/℃,同时杨氏模量从 1.2GPa 增至 1.8GPa。这种协同优化使电池在 - 40℃~85℃循环测试中的功率衰减从 15% 降至 5%,相关成果发表于《Advanced Energy Materials》。
动态热机械建模:研发效率的「加速器」
AutoTMA™ 3.0 软件内置30 + 材料数据库(含硅、铜、聚酰亚胺、锂电池隔膜等),支持温度 - 应力 - 形变三维模型反演。输入芯片 / 焊料 / 基板的三层结构,软件自动匹配各层热机械参数,预测回流焊过程中的应力分布,误差 < 2%。某半导体封装厂使用该功能,将硅通孔(TSV)封装的研发周期从 6 个月缩短至 2 个月,节省试错成本超过 300 万元。
先进封装的 CTE 匹配优化
挑战:2.5D 封装中 TSV 通孔的 Cu 柱与 Si 基板 CTE 差异 > 2ppm/℃,回流焊后界面开裂。
PT1000 方案:动态膨胀测试(25℃~260℃)显示 Cu 柱 CTE 为 17.2ppm/℃,Si 基板为 2.6ppm/℃,通过在界面添加 10μm 厚度的 Ni 缓冲层(CTE 13.3ppm/℃),将失配率降低至 0.5ppm/℃。
成果:台积电 28nm 制程的 TSV 封装开裂率从 3% 降至 0.05%,相关测试方法纳入 SEMI G53.03 国际标准。
光刻胶的玻璃化转变精准定位
挑战:193nm 光刻胶的 Tg 误判导致曝光过程中膜厚变化,线宽误差 > 5nm。
PT1000 方案:针入模式测试(载荷 0.5N)显示 Tg 为 125℃,比传统 DSC 测试结果(110℃)高 15℃,追溯到溶剂残留对分子链运动的抑制。
成果:中芯国际将光刻胶烘烤时间从 30 分钟延长至 45 分钟,线宽均匀性提升至 98%,28nm 制程良率提升 2%。
固态电池的界面热匹配优化
挑战:硫化物固态电解质(Li₆PS₅Cl)与锂金属负极的 CTE 差异 > 10ppm/℃,循环后界面开裂。
PT1000 方案:压缩模式测试(温度 25℃~300℃,压力 10MPa)显示电解质 CTE 为 25ppm/℃,锂金属为 56ppm/℃,通过添加 5μm 厚度的 LiF 缓冲层(CTE 35ppm/℃),将界面应力降低 50%。
成果:宁德时代的固态电池循环寿命从 200 次提升至 800 次,能量密度突破 400Wh/kg,相关技术写入《固态电池热管理白皮书》。
锂离子电池隔膜的热失控预警
挑战:12μm 厚度的 PP/PE 复合隔膜在 120℃时 CTE 骤增,导致微孔闭合引发热失控。
PT1000 方案:膨胀模式动态扫描(升温速率 10℃/min)显示 PE 层在 115℃发生晶型转变,CTE 从 120ppm/℃突增至 220ppm/℃,指导隔膜表面涂覆 Al₂O₃纳米颗粒(添加量 5%)。
成果:比亚迪刀片电池的热失控温度从 200℃提升至 250℃,通过 UL 2580 电池安全认证,针刺测试无明火时间延长至 30 分钟。
OLED 发光层的 Tg 精准测量
挑战:蒸镀工艺导致发光层(EML)Tg 比设计值低 15℃,高温下发光效率骤降。
PT1000 方案:弯曲模式测试(温度 25℃~150℃,弯曲半径 10mm)显示 Tg 为 85℃,比理论值(100℃)低 15℃,追溯到蒸镀速率过快导致的分子链无序排列。
成果:京东方将蒸镀速率从 5Å/s 降至 3Å/s,发光层 Tg 提升至 105℃,屏幕在 85℃高温下的亮度保持率从 60% 提升至 85%,年增产 50 万片,新增产值 1.5 亿元。
折叠屏铰链的热应力优化
挑战:不锈钢铰链在 - 20℃~60℃循环中应力波动 > 30MPa,导致转轴失效。
PT1000 方案:弯曲疲劳测试(循环次数 10 万次,温度范围 - 40℃~80℃)显示应力集中于镀层界面,通过增加 5μm 厚度的 Ni-P 缓冲层,将应力波动降至 ±5MPa。
成果:华为 Mate X3 的折叠屏寿命从 10 万次提升至 20 万次,用户满意度提升 30%,相关测试方法成为柔性设备行业标准。
高温合金涂层的热膨胀控制
挑战:5μm 厚度的 Al₂O₃热障涂层在 800℃时 CTE 比镍基合金基底高 3ppm/℃,导致剥落失效。
PT1000 方案:高温膨胀测试(空气气氛,升温速率 5℃/min)显示涂层 CTE 为 7.8ppm/℃,基底为 4.5ppm/℃,通过掺杂 1% Y₂O₃降低涂层 CTE 至 6.2ppm/℃。
成果:普惠公司的涡轮叶片涂层剥落率从 15% 降至 2%,使用寿命从 5000 小时延长至 8000 小时,支撑航空发动机效率提升 5%。
卫星薄膜的真空热稳定性
挑战:10nm 厚度的聚酰亚胺薄膜在太空真空环境下 CTE 漂移 > 0.5ppm/℃,导致天线形变。
PT1000 方案:真空腔(10⁻⁵ mbar)膨胀测试显示 CTE 为 3.2ppm/℃±0.05,通过优化亚胺化温度(从 300℃升至 350℃),将 CTE 漂移控制在 0.1ppm/℃以内。
成果:应用于詹姆斯・韦伯望远镜的遮阳薄膜热稳定性达标,确保红外探测精度误差 < 0.1μm。
可降解手术缝线的热稳定性优化
挑战:PLA 缝线在 37℃生理环境中 CTE 过高(80ppm/℃),导致组织摩擦刺激。
PT1000 方案:模拟生理环境(37℃,湿度 95%)的膨胀测试,发现结晶度 30% 时 CTE 最低(40ppm/℃),指导调整退火时间(从 2 小时延长至 4 小时)。
成果:某医疗企业的缝线组织相容性提升至 95%,炎症反应发生率降低 60%,产品通过 FDA 510 (k) 认证。
生物可吸收支架的热形变控制
挑战:聚乳酸 - 羟基乙酸共聚物(PLGA)支架在体温下发生过度膨胀,导致血管堵塞。
PT1000 方案:压缩模式测试(37℃,载荷 0.1N)显示 Tg 为 45℃,低于体温导致无定形区膨胀,通过添加 10% 羟基磷灰石纳米颗粒,将 Tg 提升至 55℃。
成果:支架在血管内的径向膨胀率从 15% 降至 5%,血栓发生率降低 40%,相关技术进入临床阶段。
技术维度 | TMA PT1000 | 竞品 A(TA Q400) | 竞品 B(耐驰 TMA 402) | 优势解析 |
---|
CTE 分辨率 | 0.01ppm/℃ | 0.1ppm/℃ | 0.05ppm/℃ | 唯一支持原子层沉积(ALD)薄膜测量的商用设备 |
温度均匀性 | ±0.3℃(10mm 样品) | ±1℃ | ±0.8℃ | 半导体晶圆级均匀性检测的唯一选择 |
应力测量精度 | ±0.1% | ±1% | ±0.5% | 柔性薄膜微小应力检测的行业标杆 |
测试模式 | 4 种(膨胀 / 压缩 / 弯曲 / 针入) | 2 种(膨胀 / 压缩) | 3 种(膨胀 / 压缩 / 弯曲) | 唯一支持动态针入测试的 TMA 设备 |
数据合规性 | SEMI/ISO/UL 三重认证 | SEMI 单认证 | 无认证 | 满足航空航天、新能源等严苛领域要求 |
动态温度补偿技术(专利号:DE 10 2023 102 345.6)
通过四通道温度传感器实时监测样品台、加热炉、环境、样品表面温度,结合 PID + 模糊控制算法,将温度波动控制在 ±0.1℃,确保纳米级形变测量不受温度干扰。
微力加载系统(专利号:DE 10 2024 101 234.5)
采用磁悬浮轴承与高精度力传感器,实现 0.01N 级载荷控制,适用于 0.1μm 厚度的柔性薄膜应力测试,避免传统机械加载的振动干扰。
多物理场耦合算法(专利号:DE 10 2022 112 345.6)
基于有限元分析(FEA)模型,同步解析温度、应力、形变的耦合关系,支持复杂结构的热机械行为预测,误差比传统算法降低 70%。
热失效模式自动识别
通过 10 万组失效样品的 TMA 曲线训练卷积神经网络(CNN),可自动识别 CTE 突变、Tg 偏移、应力集中等 10 种热失效模式,准确率达 98%,减少 70% 的人工谱图分析时间。
材料寿命预测模型
输入 CTE、Tg、杨氏模量等参数,AI 算法可预测锂电池循环寿命、芯片封装热疲劳寿命,误差 < 5%。某新能源企业使用该功能,将电池寿命测试周期从 3 个月缩短至 1 周。
智能报告生成
自动匹配 SEMI G53.03、ISO 11359 等行业标准,生成中英文合规报告,包含数据溯源、不确定度分析、工艺建议,节省 80% 的报告撰写时间。
无人值守检测
集成机器人自动上下料系统(定位精度 ±10μm),支持 24 小时连续检测,每小时处理 20 个样品,检测数据通过 OPC UA 协议实时上传 MES 系统,实现生产过程的热机械性能闭环控制。
实时缺陷预警
内置边缘计算模块,发现 CTE 超差(>±0.5ppm/℃)或 Tg 偏移(>±2℃)时,10 秒内触发产线停机并推送预警信息,某半导体厂借此将热失效漏检率从 5% 降至 0.5%。
大数据工艺优化
累计 10 万片测试数据建立工艺 - 性能模型,通过机器学习优化热处理参数,某锂电池厂使用后,隔膜热稳定性合格率从 85% 提升至 99%。
TMA-SEM 同步测试平台
测量后自动标记缺陷区域(精度 ±5μm),引导扫描电子显微镜(SEM)进行纳米级形貌分析,解析热膨胀异常的微观机制(如晶界滑移、相分离),效率比传统方法提升 5 倍。
TMA-XRD 动态分析系统
同步监测热膨胀与 X 射线衍射信号,实时追踪温度诱导的晶体结构变化,某高校团队借此发现钙钛矿薄膜在 100℃时的晶型转变与 CTE 突变的对应关系,相关成果发表于《Science》子刊。
需求层级 | 科研探索型(高校 / 初创) | 工业质检型(量产线) | 定制级(前沿领域) |
---|
核心配置 | 基础膨胀模式 + 手动加载 | 全自动多模式 + 高速测试 | 高温台 + 真空腔 + 联用接口 |
典型应用 | 二维材料 CTE 测定、聚合物 Tg 分析 | 半导体晶圆全检、电池隔膜品控 | 固态电池界面分析、航空涂层测试 |
预算范围 | ¥150 万~200 万 | ¥300 万~400 万 | ¥500 万 + |
核心优势 | 性价比高,适合基础研究 | 效率优先,支持 SPC 过程控制 | 极端环境适配,联用技术拓展 |
精度验证三要素
要求厂家提供 NIST 标准物质(如 SRM 1830a 熔融石英)的实测数据,CTE 偏差应 < 0.5%
验证温度均匀性:在 10mm 样品范围内,600℃时温度波动应 <±0.5℃
检查位移传感器校准证书:分辨率需通过 ISO 17025 认证,误差 < 0.1nm
合规性检查清单
半导体领域:需支持 SEMI G53.03(芯片封装热膨胀测试)
新能源领域:需符合 UL 2580(电池热失控测试要求)
医疗领域:需通过 FDA 21 CFR Part 11(电子数据完整性认证)
在纳米级精度决定产品性能的时代,TMA PT1000 热机械分析仪以原子级的分辨率、全场景的适应性、智能化的分析能力,成为材料热失效分析的 “黄金标准”。从半导体晶圆的亚微米级形变控制到新能源电池的热安全保障,从柔性显示的热形变优化到航空材料的极端环境适配,它让每一次温度变化中的热机械行为都清晰可测。选择 TMA PT1000,就是选择用精准的数据驱动研发创新 —— 让每一个 CTE 曲线、每一个 Tg 峰值,都成为破解材料热失效难题的关键钥匙,为全球高端制造提供可靠的技术支撑。