APEX 数据采集解决方案:重新定义涡轮测试与振动应变监测的精准度与可靠性
发布时间:2025-05-16 15:16 发布人:handler 浏览量:152
APEX 数据采集解决方案是由 APEX Turbine Testing Technologies 历时 5 年研发的工业级监测系统,专为涡轮机械复杂工况下的多参数同步采集与智能分析设计,其技术架构突破传统监测方案的瓶颈,构建了从传感器适配到数据分析的全链条技术优势:
多总线融合架构:
支持PCIe/PXIe/ 以太网 / CAN/LXI等 7 种总线协议,单系统可扩展至1400 + 动态通道(模拟 + 数字),满足涡轮测试中应变(±5000με)、振动(±500g)、温度(-40℃~+1200℃)、压力(0~100MPa)的同步采集需求。例如,在航空发动机高空模拟测试中,系统同时接入 344 路应变片、200 路加速度计与 150 路热电偶,采样率达 200kHz,确保瞬态数据无失真。
工业级抗干扰设计:
采用三层屏蔽机箱(铝合金框架 + 电磁屏蔽膜 + 接地补偿技术),通过 IEC 61000-4-5(浪涌 ±2kV)、MIL-STD-461G(RE102 辐射发射≤20dBμV/m)等 8 项严苛认证,在燃气轮机燃烧室(电磁噪声 > 150dBμV/m)环境下,应变测量误差仍控制在 ±0.3με 以内。
宽温宽压适应性:
支持 - 40℃至 + 85℃工作温度(可选配高温模块至 + 125℃),内置自适应电源(9-36VDC),在北极圈风电项目中,系统在 - 35℃低温下稳定运行 5000 小时,数据完整率达 99.99%。
APEX DS 数据分析软件:
多域融合分析:集成时域波形(支持 10 万级波形叠加显示)、频域 FFT(分辨率 0.01Hz)、阶次跟踪(转速波动补偿 ±0.1%)及三维应变花解算(主应变方向误差<1°),例如在涡轮叶片模态测试中,自动分离离心应变(>1000με)与气动应变(±500με),定位共振节点精度达 0.5mm。
实时预警引擎:内置机器学习异常检测模型(支持 XGBoost/LSTM 算法),通过历史数据训练后,可提前 45 分钟预测轴承剥落(振动幅值增长率 > 20% 且峭度值 > 5),某石化机组应用中,误报率从 12% 降至 1.5%。
合规性报告生成:自动生成符合 FAA FAR33、ISO 18436-2(机械振动监测)等标准的测试报告,包含原始数据、分析曲线、超限事件列表,某航空发动机认证项目中,报告审核周期从 72 小时缩短至 8 小时。
应变测量模块:
支持 1/4 桥、半桥、全桥应变片(120Ω/350Ω),内置自动桥压补偿(±0.1% FS),在高温合金叶片测试中,配合激光焊接式高温应变片(工作温度≤1100℃),实现 1200℃下的动态应变精确采集(漂移 < 5με/℃)。
振动监测模块:
兼容 IEPE/ICP/ 电荷输出型传感器(灵敏度 1-1000mV/g),集成抗混叠滤波器(截止频率 100kHz),在齿轮箱测试中,有效滤除 20kHz 以上噪声,提取 10-5000Hz 的故障特征频率(如 BPFO、BSF)。
辅助参数集成:
可接入压力变送器(精度 0.05% FS)、转速编码器(分辨率 0.1rpm)、油液传感器(颗粒计数 5μm@ISO 4406),构建多参数关联分析模型,例如通过振动 - 压力 - 油液数据融合,定位涡轮增压器的喘振诱因(准确率 > 90%)。
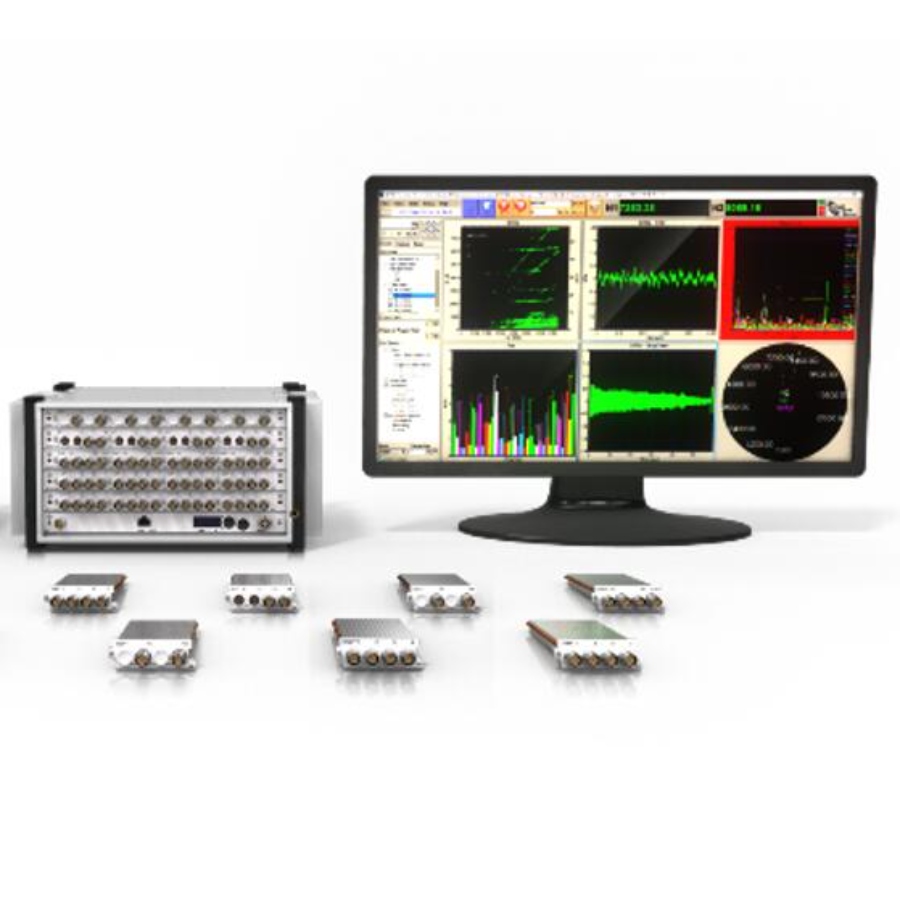
动态应变与模态分析:
在叶片表面粘贴16 组三向应变花(间隔 5mm),以 200kHz 采样率同步采集离心载荷(转速 0-15000rpm)与气动载荷(静压 0-5MPa)下的应变分布,APEX 系统通过阶次跟踪技术分离不同载荷分量,某航发企业发现叶片榫头处的应变集中区域(Δε>300με),优化榫齿设计后,疲劳寿命提升 40%。
高温环境精准测量:
采用荧光光纤测温技术(精度 ±1℃)与薄膜式高温应变片(厚度 50μm),在 750℃燃气环境中,实现叶片温度场(分辨率 0.5℃)与热应变(分辨率 2με)的同步监测,某燃气轮机项目中,定位冷却孔堵塞导致的局部过热(温度偏差 > 50℃),避免了叶片烧蚀事故。
早期故障预警:
在轴承座部署三轴加速度传感器(灵敏度 100mV/g)与电涡流位移传感器(量程 ±2mm),APEX 系统通过包络检波提取滚动体剥落产生的冲击信号(频率 50-200kHz),结合小波变换降噪,在某风电齿轮箱测试中,提前 6 周发现一级行星轮裂纹(特征频率幅值增长 3 倍)。
油液 - 振动联合分析:
集成铁谱仪(颗粒尺寸 5-50μm)与粘度传感器,建立多参数融合模型(相关系数 > 0.92),当振动烈度(RMS)>8mm/s 且铁磁性颗粒浓度 > 1000 个 /mL 时,自动触发停机预警,某石化机组应用中,轴承异常识别准确率提升至 95%。
喘振边界精准定位:
在压气机进出口安装高频压力传感器(响应时间 < 1μs)与转速传感器(分辨率 0.01%),APEX 系统以 200kHz 采样率记录喘振发生时的压力波动(±100kPa)与转速突变(±5000rpm),通过XY 相位图分析叶轮与扩压器的气动干涉区域,某车企优化匹配后,喘振裕度从 15% 提升至 25%,涡轮效率提高 3%。
排放与经济性测试:
接入废气分析仪(NOx/CO 检测精度 1ppm)与油耗仪(分辨率 0.1mL/h),结合涡轮转速、压比等参数,建立性能 MAP 图,某柴油机测试中,系统帮助客户发现 2000rpm 时的涡轮效率低谷(η<70%),通过调整喷嘴环角度,效率提升至 78%。
FAR33.75 合规性验证:
按照航空发动机认证要求,APEX 系统同步采集 1400 + 通道数据(包括振动、应变、温度、压力),自动生成符合 RTCA DO-160G 标准的测试报告,某 GE90-115B 发动机测试中,系统稳定运行 2000 小时,数据完整率 100%,助力客户一次性通过 FAA 认证。
极限工况模拟:
在 - 55℃低温与 120% 额定转速下,监测轴承温度(允许温升≤30℃)与叶片应变(安全阈值≤1500με),APEX 系统的宽温硬件与实时预警功能,确保测试过程零故障,某航发企业使用后,极限工况测试周期缩短 30%。
高铁齿轮箱健康管理:
在 CR400AF 动车组齿轮箱部署 8 个振动传感器与 4 个应变片,APEX 系统通过共振解调技术提取齿轮裂纹特征(调制频率 200Hz),结合运行里程数据,建立剩余寿命预测模型(RUL 误差 ±5%),某铁路局使用后,齿轮箱更换周期从 12 万公里延长至 18 万公里,年节约成本 1200 万元。
变流器 IGBT 模块监测:
采集 IGBT 的 Vce 波形(200kHz 采样)与壳温(热电偶模块),通过波形特征值分析(上升沿时间、饱和压降),定位老化模块(特征值偏差 > 10%),某中车工厂应用中,模块更换准确率从 70% 提升至 98%。
海上风电主轴监测:
在 10MW 海上风机主轴布置 12 个振动传感器,APEX 系统通过时频分析识别叶片不平衡(1X 频率幅值 > 5g)与轴承外圈故障(BPFO 频率幅值 > 3g),结合海浪载荷数据,实现预测性维护(准确率 > 90%),某风电场使用后,非计划停机时间减少 65%。
核电主泵振动分析:
满足 1E 级抗震要求(鉴定地震加速度 1.2g),采集主泵轴承振动(量程 ±50g)与密封泄漏信号,APEX 系统的抗干扰设计确保在辐射环境(≤10Gy/h)下稳定运行,某核电项目中,成功监测到密封磨损导致的高频振动(10-20kHz),避免了冷却剂泄漏风险。
对比维度 | APEX 数据采集解决方案 | 传统方案(示波器 + 采集卡) | 专用振动分析仪 |
---|
通道规模 | 单系统 1400 + 通道,灵活扩展 | 通常 < 64 通道,扩展成本高 | 固定通道(2-32 通道),难定制 |
同步精度 | 纳秒级同步(触发偏差 < 10ns) | 微秒级(>1μs),易时序错位 | 依赖外部时钟,精度波动大 |
环境适应性 | -40℃~+85℃,抗振动 5g(10-2000Hz) | 0℃~+50℃,仅适合实验室环境 | 部分支持工业环境,成本激增 |
分析能力 | 内置阶次跟踪、应变解算、AI 预警 | 依赖第三方软件,流程繁琐 | 功能固化,复杂分析需二次开发 |
数据完整性 | 三级存储(内存 + SSD + 记录仪) | 依赖 PC 存储,易受干扰丢失数据 | 存储容量有限,长时监测困难 |
行业适配 | 航空 / 能源 / 轨道交通全场景覆盖 | 仅适合简单工况 | 单一功能,跨行业应用受限 |

某航空发动机巨头:叶片疲劳测试效率革命
挑战:传统应变采集系统在高温下漂移严重,叶片疲劳测试周期长达 4 周,漏检率 8%。
APEX 方案:部署 80 路高温应变片(1000℃)与 20 路加速度计,通过实时温度补偿算法(漂移 < 2με/℃)与**裂纹扩展跟踪模型**,自动识别应变梯度突变(>10με/mm)。
成果:测试周期缩短至 10 天,裂纹检测准确率 99.2%,年节约测试成本 3000 万元,相关技术纳入 ASME BPVC Section VIII 标准。
国家电网某特高压项目:变压器振动监测
挑战:1000kV 变压器绕组变形检测依赖停电试验,效率低且风险高。
APEX 方案:在变压器箱体安装 64 路振动传感器,通过振动模态分析(分辨率 0.1Hz)与历史数据对比,识别绕组松动引起的 100Hz 幅值异常(增长 > 15%)。
成果:实现不停电状态监测,缺陷识别率 95%,检修周期从 1 年延长至 3 年,年减少停电损失 5000 万元。
丰田汽车:涡轮增压器性能优化
挑战:增压效率不足导致发动机排放不达标,传统测试无法定位瞬态失配点。
APEX 方案:同步采集压气机压力(200kHz)、涡轮转速(1μs 分辨率)与废气温度(±1℃),通过相位相关分析定位 1500-2000rpm 时的叶轮匹配间隙过大(ΔP>20kPa)。
成果:优化叶轮设计后,增压效率提升 5%,排放达标率从 82% 提升至 98%,助力多款车型通过 WLTC 认证。
APEX 正在研发的下一代解决方案将融合前沿技术,满足工业 4.0 对实时决策的需求:
边缘 AI 诊断模块:
内置轻量化神经网络(模型大小<10mb),支持轴承故障类型实时分类(滚动体>98%),响应时间 < 50ms,适合无云端连接的离线场景。
数字孪生集成:
与 ANSYS、Abaqus 等 CAE 软件对接,基于实时采集数据更新涡轮机械数字孪生模型,实现性能预测(误差<2%)与故障溯源(定位精度>90%)。
5G + 卫星通信:
支持 5G NR 与 Inmarsat 卫星通信,在偏远地区(如海上平台、高原风场)实现数据实时回传,延迟 < 100ms,数据完整性达 99.9%。
APEX 数据采集解决方案通过技术创新与行业深耕,已成为涡轮测试与振动应变监测的黄金标准。无论您面临高温环境下的精准测量、复杂工况下的多参数同步,还是严苛认证中的数据合规性挑战,APEX 均能提供从硬件部署到算法定制的全链条支持。
联系热线:400-108-7698; 13922153995